There are many safety risks associated with working in warehouses, and despite high levels of compliance in the UK, there continues to be work-related fatalities and serious injuries every year. The latest statistics from the HSE reveal that in the reporting period 2022/23, 15 workers lost their lives and a further 29,000 sustained non-fatal injuries in the transportation and storage industry.
The most common risks of safety in Warehousing are:
- Slips, trips and falls (33% of all reported non-fatal injuries*)
- Being struck by a moving vehicle (37% of all fatal injuries*)
- Fall from height (19% of all reported non-fatal injuries*)
- Being struck by a moving or falling object (16% of all fatal injuries*)
- Handling, Lifting and carrying (21% of all reported non-fatal injuries*)
Points to consider when managing safety in warehousing:
1) Take worker fatigue seriously
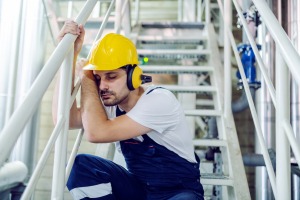
Fatigue creates safety risk in any workplace, however, in warehouses, the impact of fatigue can have potentially life-threatening consequences. Workers who undertake constant physical activity throughout their shift will suffer increased fatigue. Unsurprisingly, injuries are more likely to occur in the later hours of a shift as worker concentration and safety awareness reduces.
2) Stack smartly
Optimising stock control and maximising storage capacity are clearly critical success factors in managing the commercial and financial performance of businesses in this industry, however, space planning must take into consideration safety in warehousing factors.
Warehouse stock levels can often vary greatly, with a finite amount of space for storage, it is essential this space is used as efficiently as possible to maximise storage capacity. This can, however, result in some safety issues, specifically stacking.
3) Plan workspaces carefully and use signage prominently
Pedestrians and vehicles have to be able to circulate safely. Workplace traffic routes should be suitable for the people and vehicles using them. Where vehicles and pedestrians use the same traffic route, there should be adequate separation between them designating tracks for vehicles. This also improves the allocation of resource and ensures staff in each area have sufficient training to carry out their role safely and effectively.
Signs and floor markings should be clearly placed around the warehouse to warn of hazardous areas and indicate where PPE is needed.
4) Address ergonomic risks
When evaluating the risks to safety in warehousing related to an activity, factors to consider should include:
- Risks in the lift (bending, twisting, reaching overhead, working in awkward positions, repetitive motions)
- The load (heavy, large, unstable, difficult to grasp)
- The environment (long-distance, unclear path, poor flooring, low lighting levels)
- The individual (untrained, medical history, age-related precautions, learning difficulties, pregnant workers)
5) Follow good housekeeping rules
Keeping your warehouse tidy can be an underestimated element of safety management. As well as keeping the warehouse clean, the removal of obstructions and other hazards will reduce the likelihood of accidents and improve visibility, allowing for better anticipation of dangers. This will also help to improve the efficiency of the warehouse, improving operational performance.
6) Forklift best practices
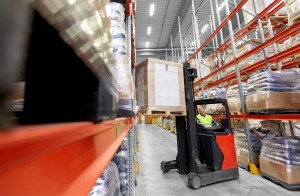
Despite their usefulness, there is no doubt forklifts are one of the most dangerous pieces of equipment in a warehouse – according to the British Safety Council, around 1,300 UK employees are hospitalised each year with serious injuries following a forklift accident. Having a forklift policy in place is crucial to preventing injury and maintain compliance. It is also important that all forklifts are properly maintained and regularly inspected for faults. It goes without saying that only those who are sufficiently trained to use forklifts should do so.
7) Ensure warehouses are well-lit.
Good lighting plays an important part in managing safety-related risks. Appropriate lighting, without glare or shadows, can reduce eye fatigue and headaches. It highlights moving machinery and other safety hazards. It also reduces the chance of accidents and injuries from ‘momentary blindness’ while the eyes adjust to brighter or darker surroundings.
8) Carry out regular equipment checks
All equipment and vehicles should be maintained in a safe condition and should be inspected and tested regularly to ensure they are safe to use. It is essential that only trained employees use machinery and that machine guards are installed where appropriate.
9) Emergency equipment
Even if you have robust safety processes in place, accidents will still happen. It is important to prepare for the worst and ensure all employees know what to do in the event of an emergency. Essential items include first aid kits and fire extinguishers as well as any relevant PPE depending on the types of products stored.
10) Encourage engagement and involvement and ensure all employees have the appropriate training
Employee engagement is essential to building a strong safety culture within a business, especially in high-risk environments. It is important employees are fully aware of the risks in their workplace and nullify any hazards before they result in an accident, reporting any near misses they see. You also have a legal responsibility to ensure that all workers are appropriately trained, not only in general health and safety but also training specific to the task/equipment and associated risks. Safe systems of work should complement training and not be relied on as a substitute.
How can we help?
The SaaS-based health and safety software AssessNET is a modular solution covering all facets of health and safety ranging from Risk Assessments, Hazard Reporting, Manual Handling, Health and Safety Training and more than 15 other aspects.
Book your personal demonstration today. We have a variety of ways to bring our software to life and demonstrate how it supports businesses to manage risk effectively. Whether you’d like a video demonstration or prefer a live call with one of our specialists, complete the form and we’ll be in touch!
*source: HSE Transportation and Storage Statistics in Great Britain, 2020.